Продолжая использовать сайт, вы даете свое согласие на работу с этими файлами.
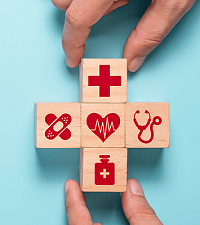
جوشکاری

جوشکاری (به انگلیسی: Welding) یکی از روشهای ساخت میباشد که هدف آن اتصال دائمی مواد مهندسی از قبیل فلز، سرامیک، پلیمر و کامپوزیت بهیکدیگر است؛ و این کار معمولاً از طریق ایجاد حرارت بالا و ذوب ماده و سپس سرد کردن برای ایجاد جوش انجام میشود. جوشکاری با روشهای اتصال دما پایینتری مانند لحیمکاری نرم (Soldering) و لحیمکاری سخت (Brazing) که در آنها فلز پایه ذوب نمیشود، تفاوت دارد.
در جوشکاری علاوه بر ذوب فلز پایه، معمولاً از یک ماده به عنوان پرکننده نقطه اتصال (Filler) استفاده میشود تا حوضچه ای از مواد مذاب ایجاد گردد که پس از خنک شدن و ایجاد اتصال میتواند از فلز یا ماده پایه نیز قوی تر باشد. همچنین ممکن است از فشار در کنار گرما یا به تنهایی برای تولید جوش استفاده گردد. ضمناً در جوشکاری به نوعی محافظ برای حفاظت از فلزات پرکننده یا فلزات ذوب شده در برابر اکسید شدن یا آلودگی نیاز است.
برای ایجاد حرارت مورد نیاز جوشکاری از منابع انرژی متعددی میتوان استفاده کرد، از قبیل: شعله گاز، قوس الکتریکی، لیزر، پرتوی الکترون، اصطکاک، و امواج مافوق صوت. همچنین جوشکاری در محیطهای صنعتی مختلفی قابل اجراست از قبیل: هوای آزاد، جوشکاری زیر آب، و خارج از اتمسفر زمین. جوشکاری یک کار خطرناک است و برای جلوگیری از سوختگی، شوک الکتریکی، آسیب چشمی و دید، استنشاق گازهای سمی و دود و قرار گرفتن در معرض اشعه ماوراء بنفش شدید، نیاز به احتیاط میباشد.
پیشینه
تا اواخر قرن نوزدهم، تنها فرایند جوشکاری موجود، جوشکاری توسط آهنگری بود که آهنگرها بیش از هزار سال از آن استفاده میکردند. جوشکاری قوس الکتریکی (جوش برق) و جوشکاری اکسی-استیلن (جوش گاز) از اولین فرآیندهای توسعه جوشکاری در اواخر قرن گذشته بودند. پس از آن خیلی زود فرایندهای جدیدی از قبیل جوش مقاومت الکتریکی ابداع شدند. در خلال سالهایی که جنگهای جهانی رخ داد، به دلیل نیاز شدید به روشهای سریع و مطمئن ایجاد اتصال، فرایندهای جوشکاری با سرعت بسیار زیادی رشد کردند. پس از جنگ جهانی روشهای مختلفی از قبیل روشهای دستی جوشکاری مانند جوشکاری با الکترود دستی پوششدار (جوش برق)، که امروزه یکی از متداولترین روشهای جوشکاری محسوب میشود، و روشهای نیمه و تمام اتوماتیک از قبیل جوشکاری قوسی با گاز محافظ (جوش آرگون یا CO2)، جوشکاری زیرپودری، جوش قوسی Flux-cored و جوش سربار الکتریکی ابداع شدند. امروزه دانش همچنان در حال توسعه بوده و رباتهای جوشکاری یکی از اجزای اصلی بسیاری از کارخانجات محسوب میشوند.
در سال ۱۸۰۰، سر همفری دیوی قوس الکتریکی ضربان-کوتاه را کشف کرد و نتایج خود را در سال ۱۸۰۱ منتشر کرد. در سال ۱۸۰۲، واسیلی پتروف، دانشمند روسی، قوس الکتریکی مداوم را ایجاد کرد، و متعاقباً «اخبار آزمایشهای گالوانیک - ولتاییک» را در سال ۱۸۰۳ منتشر کرد، و در آن آزمایشهای انجام شده در سال ۱۸۰۲ را توصیف کرد. یکی از مواردی که این گزارش منتشر شده بسیار مهم بود، توصیف قوس الکتریکی پایدار و توصیف کاربردهای احتمالی آن از جمله ذوب فلزات بود. در سال ۱۸۰۸، دیوی که از کار پتروف بیخبر بود، دوباره قوس الکتریکی مداوم را کشف کرد. در سالهای ۱۸۸۱–۸۲ نیکلای بناردوس (روسی) و استنیسلاو اولسفسکی (لهستانی) اولین روش جوشکاری قوس الکتریکی را با استفاده از الکترودهای کربن به نام جوشکاری قوس کربن ایجاد کردند. پیشرفت در جوشکاری قوس الکتریکی با اختراع الکترودهای فلزی در اواخر دهه ۱۸۰۰ توسط یک شخص روسی، به نام نیکلای اسلاویانوف (۱۸۸۸) و یک شخص آمریکایی به نام چارلز. ال. کافین (۱۸۹۰) ادامه یافت. در حدود سال ۱۹۰۰، آ. پی. استرومنگر در بریتانیا یک الکترود فلزی روکش دار ارائه کرد، که قوس پایدارتری را به وجود آورد. در سال ۱۹۰۵، دانشمند روسی ولادیمیر میتکویچ پیشنهاد کرد که از یک قوس الکتریکی سه فاز برای جوشکاری استفاده شود. جوشکاری جریان متناوب توسط سی. جی. هولسلگ در سال ۱۹۱۹ اختراع شد، اما تا یک دهه بعد محبوبیت پیدا نکرد.
فرایندهای جوشکاری
فرایندهای جوشکاری با قوس الکتریکی
جریان الکتریکی از جاریشدن الکترونها در یک مسیر هادی بهوجود میآید. هرگاه در مسیر مذکور یک شکاف هوا (گاز) ایجاد شود، جریان الکترونی و در نتیجه جریان الکتریکی قطع خواهد شد. چنانچه شکاف هوا بهاندازهٔ کافی باریک بوده و اختلاف پتانسیل و شدت جریان بالا، گاز میان شکاف یونیزهشده و قوس الکتریکی برقرار میشود. از قوس الکتریکی بهعنوان منبع حرارتی در جوشکاری استفاده میشود. حرارت ایجاد شده در جوشکاری به دلیل حرکت الکترونها در ستون قوس و بمباران الکترونی قطعه کار میباشد. روشهای جوشکاری با قوس الکتریکی عبارتاند از:
- جوشکاری با الکترود دستی پوششدار (Shielded Metal Arc Welding-SMAW)
- جوشکاری زیرپودری (submerged arc welding-SAW)
- جوشکاری با گاز محافظ (GMAW یا MIG/MAG)
- جوشکاری با گاز محافظ و الکترود تنگستنی (GTAW یا جوشکاری TIG)
- جوشکاری پلاسما
فرایندهای جوشکاری مقاومتی
در جوشکاری مقاومتی با عبور یک جریان الکتریکی بالا از درون قطعه کار، و ایجاد گرما به دلیل وجود مقاومت الکتریکی و فشار وارد شده از سمت بازوهای مسی اتصال ایجاد میگردد. با عبور جریان زیاد (۱۰۰۰ تا ۱۰۰۰۰ آمپر) از درون فلز، حوضچه کوچکی از فلز مذاب در منطقه جوش ایجاد میشود. بهطور کلی، روشهای جوشکاری مقاومتی کارآمد هستند و آلودگی کمی ایجاد میکنند، اما کاربرد آنها تا حدودی محدود است و هزینه تجهیزات میتواند زیاد باشد. روشهای جوشکاری مقاومتی عبارتند از:
- جوش نقطهای
- درز جوش
- جوش تکمهای
- با استفاده از قالب
فرایندهای جوشکاری حالت جامد
دستهای از فرایندهای جوشکاری هستند که در آنها عمل جوشکاری بدون ذوبشدن لبهها انجام میشود. در واقع لبههای تحت فشار با حرارت یا بدون حرارت در همدیگر له میشوند. فرایندهای این گروه عبارتاند از:
در این روش بهجای استفاده از انرژی الکتریکی برای تولید گرمای مورد نیاز ذوب فلزات از انرژی مکانیکی استفاده میگردد. بهاین ترتیب که یکی از دو قطعه که با سرعت درحال دوران است بهقطعهٔ دوم که ثابت نگه داشتهشده تماس داده میشود. در اثر اصطکاک بین دو قطعه و تولید حرارت، محل تماس دو قطعه ذوبشده و لبههای تحت فشار با حرارت در همدیگر له میشوند.
فرایند جوشکاری با گاز
جوشکاری با گاز یکی از گروه فرایندهای جوشکاری است که در آن، اتصال با ذوبشدن توسط یک یا چند شعله مانند استیلن یا پروپان، با اعمال فشار یا بدون آن، با کاربرد فلز پرکننده یا بدون آن انجام میشود.
از لیزرهای مختلفی مانند «زر گاز کربنیکی» یا لیزر یاقوت برای جوشکاری میتوان استفاده کرد. دقت میشود که انرژی پرتو، آنقدر زیاد نباشد که باعث تبخیر فلز شود.
جوشکاری با اشعه الکترونی
کاربرد جریانی از الکترونها است که با ولتاژ زیاد شتاب داده شدهاند و بهصورت باریکهای متمرکز بهعنوان منبع حرارتی جوشکاری بهکار میروند. بهدلیل چگالی بالای انرژی در این پرتو، منطقه تفدیده بسیار باریک میباشد و جوشی با کیفیت مناسب بهدست میآید. این فرایند بهعنوان اولین فرایند جوشکاری بهکاررفته برای ساخت بدنهٔ جنگندهها استفاده شد.
دستگاه جوش و پیچ جوش
دستگاه پیچ جوش یکی از ابزارهای اصلی صنعت جوشکاری است. این دستگاه، نوعی دستگاه جوش است که در طول فرآیند جوشکاری از مهارت کارگر یا جوشکار به گونه ای کمک می کند که بتوان همه چیز را بدون هیچگونه خطا و به یک شکل صحیح جوش داد.
از دستگاه پیچ جوش در بسیاری از صنایع مانند خودروسازی، صنایع دریایی، صنایع مکانیکی و صنایع فضایی استفاده می شود. این دستگاه باعث کاهش زمان جوشکاری، افزایش کارایی و کاهش احتمال خطا می شود.
تاریخچه دستگاه پیچ جوش به سال ۱۹۴۰ برمی گردد. در آن زمان، دستگاه پیچ جوش به صورت دستی ساخته می شد و برای جوش دادن پیچ های فلزی از آن استفاده می شد. اما با توسعه فناوری جوشکاری، دستگاه پیچ جوش نیز بازطراحی و به شکلی اتوماتیک و مکانیزه تبدیل شد.
پیچ جوش به عنوان یک روش پیوند دهی بین دو قطعه فلزی بسیار مفید است. این روش به صورت خودکار و با استفاده از دستگاه جوش انجام میشود و نسبت به روشهای دیگر پیوند دهی مانند پیچ گارانتی شده و فارغ از هیچگونه شیوع ایجاد شده توسط بازسازیهای دورهای یا بروزرسانیهای لازم، قابلیت مقاومت و ایمنی بیشتری را در پیچهای همراه با خود دارد.
دستگاه جوش دستگاهی است که برای پیوند دهی دو قطعه فلزی استفاده میشود. در واقع این دستگاه از اتصال الکتریکی بین قطب های مختلف بهره میبرد تا در نتیجه گرمای تولید شده این دو قطعه فلزی به هم متصل شوند.
هندسه
اتصالهای جوشی را از لحاظ هندسی میتوان به شکلهای گوناگونی آماده کرد. ۵ گونه اصلی اتصالهای جوشی از لحاظ هندسی عبارتند از:
- جوش لب به لب (butt joint)
- جوش روی هم (lap joint)
- جوش گوشه ای (corner joint)
- جوش لبه ای (edge joint)
- جوش T شکل (T-joint)
روشهای دیگری برای آمادهسازی لبه قطعات قبل از جوشکاری وجود دارد. از قبیل: V شکل، U شکل، J شکل.
در بعضی روشهای جوشکاری لازم است که اتصالها حتماً به شکل خاصی آماده شوند. برای مثال در جوشکاری درزی یا نقطه جوش زنی یا جوشکاری پرتو الکترونی باید حتماً دو قطعه روی هم قرار داده شده و جوشکاری شوند یا در اصطلاح جوشکاری روی هم (Lap joint) شوند. بعضی روشهای دیگر مانند جوشکاری قوسی فلز پوششدار (جوش برق) بسیار منعطف بوده و تقریباً با این روش میتوان هر نوع اتصالی را جوشکاری کرد. در برخی فرایندهای جوشکاری برای پر کردن شیار چند مرحله مختلف جوشکاری میشوند که به هر مرحله اصطلاحاً «پاس» میگویند. در این حالت پس از هر پاس جوشکاری اجازه میدهند که قطعه خنک شده و سپس یک مرحله یا پاس دیگر آن را جوشکاری میکنند.
اثرات گرما
متالورژی جوشکاری
گرمایش و سرمایش از مولفههای اصلی اکثر فرایندهای جوشکاری است. این گرمایش و سرمایش معمولاً اثرات نامطلوبی بر روی متالورژی مواد دارد. در جوشکاری ذوبی، گرما به حدی است که میتواند مقداری از فلز پایه را ذوب کرده (ماده ای که در حال جوشکاری است)، و در ادامه معمولاً یک خنک کاری سریع اتفاق میافتد. اثرات حرارتی برای این نوع جوشکاری بسیار بارز است، اما در فرایندهایی که گرمایش-سرمایش با سرعت و شیب کمتری اتفاق میافتد کمتر است. اگر به اثرات حرارتی به حد کافی توجه شود، معمولاً میتوان این اثرات نامطلوب را کاملاً از بین برده یا آن را به حداقل رساند، و به جوشی با کارایی فوقالعاده دست پیدا کرد.
از آنجایی که حوضچه مذاب معمولاً نسبت به قطعه اصلی کوچک است، جوشکاری ذوبی را میتوان به عنوان "یک قطعه ریختگی کوچک در داخل یک قالب بزرگ" در نظر گرفت. خواص و ترکیب ماده نهایی حوضچه جوش، مخلوطی است از ماده مادر و الکترود یا سیم جوش. نسبت این مواد بستگی به عواملی از قبیل نوع فرایند جوشکاری، شکل اتصال، و آمادهسازی لبه قطعات دارد.
از آنجایی که ترکیب شیمیایی این ناحیه و فرایند ذوب و انجماد آن با باقی فلز مادر متفاوت است، نمیتوان انتظار داشت که خواص آن با فلز اصلی یکسان باشد. در نتیجه برای دستیابی به خواص مکانیکی مطلوب باید فیلر یا الکترودی انتخاب شود که خواص آن در حالت «پس از ذوب و انجماد» برابر یا بالاتر از فلز مادر باشد. به همین دلیل در بسیاری از موارد ترکیب شیمیایی الکترود یا فیلر کمی با فلز مادر متفاوت است. ساختار دانهها در ناحیه ذوب شده میتواند ریز یا درشت، هم محور (equiaxed) یا ریشه درختی (dendritic)، باشد و این بستگی به نوع و حجم فلز جوشکاری و نرخ خنک کاری دارد، اما ترکیب شیمیایی اکثر الکترودها و سیم جوشها تمایل دارند دانههایی ریز و هم محور تولید کنند. برابری یا بالاتر بودن استحکام الکترودها و سیم جوشها از فلز مادر در حالت پس از جوشکاری، مبنای بسیاری از استانداردها و مشخصات فنی تعیین شده توسط AWS (انجمن جوشکاری آمریکا) است.
حوضچه فلز مذاب ایجاد شده در اثر جوشکاری ذوبی مستعد همه مشکلات و نقایص مربوط به ریختهگری فلزات، مانند تخلخل گاز، ناخالصیها، حفره گاز، ترک و انقباض است. از آنجا که معمولاً مقدار فلز مذاب در مقایسه با جرم کل قطعه کار کم است و فلز اطراف آن رسانش گرمایی خوبی دارد، انجماد و خنک سازی سریع فلز نیز کاملاً رایج است. از نقایص مرتبط با این شرایط نیز میتوان به دام انداختن گازهای محلول (تخلخل گازی)، تفکیک شیمیایی، تغییر اندازه دانه، مشکلات شکل دانه و اثرات جهتگیری اشاره کرد.
منطقه متأثر از گرما
در مجاورت حوضچه مذاب و کاملاً در داخل فلز پایه، تقریباً همیشه، ناحیه یا منطقه ای تحت عنوان منطقه متأثر از گرما (به انگلیسی: heat-affected zone) وجود دارد. در این ناحیه، که معمولاً به اختصار HAZ خوانده میشود، فلز مادر ذوب نشده، اما برای مدت زمانی کوتاه دمای آن بسیار بالا رفتهاست. فلز مجاور ممکن است حرارت کافی برای تغییر در ساختار و خواص از قبیل: تبدیل فاز، تبلور مجدد، رشد دانه، رسوب یا درشت سازی رسوبی، تردی یا حتی ترک خوردگی، جذب کرده باشد. به دلیل ساختار تغییر یافته، ناحیه متأثر از گرما ممکن است دیگر از خواص مطلوب ماده اصلی برخوردار نباشد و از آنجا که ذوب نشدهاست، نمیتوان خواص آن را مشابه حوضچه جامد شده در نظر گرفت. در نتیجه، منطقه متأثر از گرما اغلب ضعیفترین منطقه در اتصال جوشی است. به جز در مواردی که نقص آشکاری در حوضچه جامد شده وجود دارد، بیشتر شکستهای جوشکاری در منطقه متأثر از گرما ایجاد میگردد.
معمولاً اگر خواص ایجاد شده پس از جوشکاری مطلوب نباشد، خواص و ساختار کل سازه جوشکاری شده توسط عملیات حرارتی اصلاح میگردد.
پیش گرم کردن
یک روش جایگزین برای کاهش اختلاف در ریزساختار یا شدت تندی آن، پیش گرم کردن (Preheat) کل فلز پایه، یا حداقل ۱۰ سانتیمتر (۴ اینچ) از دو طرف اتصال است که دقیقاً قبل از شروع جوشکاری انجام میشود. این گرمایش باعث کاهش سرعت خنک کاری حوضچه جوش و فلز مجاور آن در منطقه متأثر از گرما میشود. خنک کاری آهسته باعث ایجاد ساختاری نرمتر و شکل پذیرتر شده و همچنین برای دفع-واپخشی هیدروژن مضر حل شده، زمان بیشتری فراهم میکند. تنشهای جوشکاری در ناحیه بزرگتری تقسیم شده و در نتیجه میزان اعوجاج یا تابیدگی قطعه و همچنین احتمال ترک خوردگی جوش کاهش مییابد.
پیش گرم کردن در فولادهای پرکربن و آلیاژی متداول تر است، و مخصوصاً در فلزاتی مانند مس و آلومینیم که رسانایی گرمایی بالایی دارند بسیار مهم است. در غیر اینصورت نرخ خنک کاری میتواند بسیار بالا باشد. از آنجا که فولادهای آلیاژی دارای سختی پذیری بالاتری هستند، احتمال تشکیل مارتنزیت در این مواد بالاتر است. هنگام جوشکاری فولادهای پرکربن و آلیاژی ممکن است چرخههای حرارتی ویژه ای، قبل و بعد از جوشکاری مورد نیاز باشد (پیش گرم و پس گرم (Postheat) کردن). برای فولادهای کربنی ساده، معمولاً دمای پیش گرم ۱۰۰ تا ۲۰۰ درجه سلسیوس مناسب است. از آنجا که میتوان فولادهای کم کربن و کم آلیاژ را بدون پیش گرم یا پس گرم کردن جوش داد، این مواد در جوشکاری بسیار استفاده میشوند.
تنشهای القایی توسط گرما
یکی دیگر از اثرات گرمایش و خنک کاری، ایجاد تنشهای پسماند است. در جوشکاری این پدیده میتواند دو گونه باشد و بیشتر در جوشکاری ذوبی که از گرمای زیادی در آن استفاده میشود، اتفاق میافتد. اثرات آنها را میتوان به صورت تغییرات ابعادی، اعوجاج و ترک خوردگی مشاهده کرد. تنشهای پسماند جوشکاری به دلیل جلوگیری از انبساط و انقباض حرارتی اتفاق میافتند. تنشهای واکنشی، تنشهای پسماندی هستند که معمولاً در قطعات نیمه تمام یا تعمیرات جوشکاری ایجاد میشوند و میتوانند باعث ترک برداشتن جوش گرم یا ایرادی در سایر مراحل استفاده گردند.
قابلیت جوشکاری یا اتصال
همه مواد مهندسی قابلیت جوشکاری توسط هر نوع فرایند جوشکاری را ندارند. هر چند که این مقیاس تقریباً مبهم است، اما معمولاً از عبارت "قابلیت جوشکاری" یا "قابلیت اتصال" برای تعیین امکان جوشکاری یک ماده در اتصال توسط جوشکاری استفاده میشوند. استفاده از یک فرایند جوشکاری میتواند نتایج فوقالعاده ای بدست دهد، در حالیکه استفاده از فرایندی دیگر ممکن است باعث یک اتصال ضعیف شود. تغییر پارامترهایی از قبیل نوع ماده الکترود، گاز محافظ، سرعت جوشکاری و نرخ خنک کاری میتواند کیفیت یک فرایند را بشدت تغییر دهد.
ماده | جوشکاری قوسی | جوشکاری هواگاز | جوشکاری
پرتو-الکترون |
جوشکاری
مقاومتی |
لحیم کاری
سخت |
لحیم کاری | اتصال چسبی |
---|---|---|---|---|---|---|---|
چدن | متداول | توصیه شده | کاربرد ندارد | به ندرت | دشوار است | کاربرد ندارد | متداول |
فولاد کربنی
و کم آلیاژ |
توصیه شده | توصیه شده | متداول | توصیه شده | توصیه شده | دشوار است | متداول |
فولاد زنگ نزن | توصیه شده | متداول | متداول | توصیه شده | توصیه شده | متداول | متداول |
آلومینیم و منیزیم | متداول | متداول | متداول | متداول | متداول | به ندرت | توصیه شده |
مس و آلیاژهای آن | متداول | متداول | متداول | متداول | توصیه شده | توصیه شده | متداول |
نیکل و آلیاژهای آن | توصیه شده | متداول | متداول | توصیه شده | توصیه شده | متداول | متداول |
تیتانیم | متداول | کاربرد ندارد | متداول | متداول | دشوار است | به ندرت | متداول |
سرب و روی | متداول | متداول | کاربرد ندارد | دشوار | کاربرد ندارد | توصیه شده | توصیه شده |
ترموپلاستیکها | ابزار داغ توصیه میشود | گاز داغ توصیه میشود | کاربرد ندارد | القا متداول است | کاربرد ندارد | کاربرد ندارد | متداول |
ترموستها | کاربرد ندارد | کاربرد ندارد | کاربرد ندارد | کاربرد ندارد | کاربرد ندارد | کاربرد ندارد | متداول |
الاستورمرها | کاربرد ندارد | کاربرد ندارد | کاربرد ندارد | کاربرد ندارد | کاربرد ندارد | کاربرد ندارد | توصیه شده |
سرامیکها | کاربرد ندارد | به ندرت | متداول | کاربرد ندارد | کاربرد ندارد | کاربرد ندارد | توصیه شده |
فلزهای ناهمسان | دشوار است | دشوار است | متداول | دشوار است | متداول/دشوار است | توصیه شده | توصیه شده |
کنترل کیفیت و بازرسی
طبق طبقهبندی استانداردهای مدیریت کیفیت (ایزو ۹۰۰۰) جوشکاری جزء فرایندهای ویژه طبقهبندی شدهاست که این نشاندهندهٔ این است که برای کنترل کیفیت و تضمین کیفیت این فرایند ویژه میباید پیشبینیهای خاصی انجام داد. به این منظور پیش از عملیات جوشکاری تمام پارامترها دخیل در فرایند شامل مواد اولیه (آلیاژها)، دستگاه و تنظیمات آن، مواد مصرفی و جوشکار بر طبق استاندارد (ایزو ۳۸۳۴) مورد ارزیابی و بررسی و تأیید قرار میگیرند.
جستارهای وابسته
![]() |
در ویکیانبار پروندههایی دربارهٔ جوشکاری موجود است. |
کتابخانههای ملی | |
---|---|
سایر |